At Fox, ‘Quality belongs to everyone’
Being close to OEMs allows for quick turnaround time
A sign on the Powersports OE assembly line at Fox reads “Everyone is an inspector.” It’s a reflection of the high expectations the company has of itself and its employees. Fox seeks to produce the highest quality parts possible in order to make its OEM clients and aftermarket customers happy.
That drive can be felt throughout the Watsonville, Calif., factory at which powersports, bicycle, truck and hot rod shocks are assembled. A tour of how product moves through the facility reveals just how stringent Fox is.
At the Powersports OE assembly line, new products first go to the Viper line, where a few employees master each product’s assembly and debug the process before passing it on to the larger assembly line. Then, once it reaches the primary line, each piece is carefully put together using detailed diagrams, and each staff member has the power to stop the line if something is found to be defective.
“We are very focused on quality and efficiency as a group,” said Juan Hernandez, Fox day supervisor. “Quality belongs to everyone.”
During shock assembly, product can be pulled randomly off the line at any point for inspection. The quality control department tests every part of random shocks — and forks on the bicycle side — and assures the size and shape of each is exact.
Once each shock makes it through assembly, it sits on a rack for 24 hours to assure no leaks are present. After that, they each go through a compression test before being packaged. But that’s not where the precise efficiency ends. The shipping department is highly organized, as OEMs need products to arrive on time, so they don’t hold up production of any vehicle, but also not too early, so the OEM doesn’t have to find room to store the shocks.
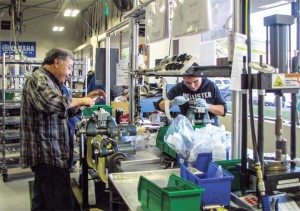
Because the whole process is so precise, Fox sees less than 1 percent of its product returned due to factory defects.
“Our quality is unparalleled,” said Mark Larson, vice president and general manager of Fox’s Powersports Division.
Fox takes pride in its American facilities. In addition to the Watsonville plant, Fox also has facilities in El Cahon, Calif., and Baxter, Minn. The company’s headquarters were moved from Watsonville to nearby Scotts Valley, Calif., in 2012 to accommodate growth at the factory. Fox is also building a facility in Taiwan, though that factory will only serve the Bicycle Division, bringing Fox closer to most bicycle manufacturers.
Keeping the Powersports and Off-Road (truck) assembly in the U.S. provides Fox opportunities it wouldn’t have otherwise.
“The manufacturers that we deal with are so competitive that one of our main points of differentiation from some of our competitors is being able to react to their requirements quickly, and we do that,” Larson said. “That’s why we set up Baxter, for example. We wanted to have a hub where we could be within a four-hour drive of one of our customers for testing reasons, for joint tuning trips, if they so want us there.”
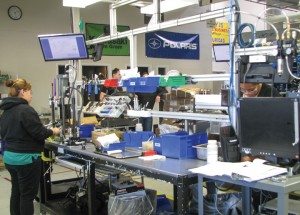
Fox’s OEM clients include Arctic Cat, BRP, John Deere, Kawasaki, Polaris, Indian and Yamaha — most of which assemble their vehicles in North America. Because of that, Fox not only assembles all of its powersports shocks in the U.S., but the company has also begun machining more of its own components. The machine shop in California, for example, runs 24 hours per day seven days per week pushing out core parts for the shock absorbers.
“What we found is when we started bringing some of our core production back to California into our machine shop, for example, where we’re making machined parts, that turnaround time is quicker, and that turnaround time led to additional business gains, which led to more opportunities, which led to quicker turnaround times, which led to more business gains, and we just said, ‘Wow, it’s easier just to have some of those core parts built here,’” Larson explained.
Shorter turnaround time allows Fox to build quick prototypes for OEMs, allowing the manufacturers to get their products — and different variations of each machine with different shock packages — out to the public swiftly. That, along with Fox’s tuning expertise, draws big OEM clients to the company.
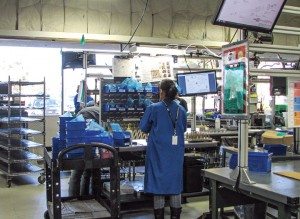
“We go race every weekend, and we tune at every race track every single weekend. Off-Road, there’s 70 events per year; Powersports there’s 56, give or take, and at each of those events, we have tuners that try to get that racer onto the podium,” Larson said. “Those same guys in each of their respective markets are the same guys that go tune with the OEMs to get that vehicle as good as it can be, so not only do we learn how to tune on the weekends, we apply that knowledge to the OE testing in the field.”
Because of Fox’s extensive race testing, the company has been able to trim many five-day OEM test sessions down to two, saving time and money for both companies.
In addition to race day testing, Fox also experiments in the aftermarket. Though the OEM business represents a larger portion of Fox’s business, the aftermarket allows the company to build its brand and try new shock concepts.
“The aftermarket drives everything. That’s what creates the brand. The aftermarket as a component to sales is smaller than the OE component, but the only reason I think we have OE business is because we have a strong aftermarket,” Larson said.
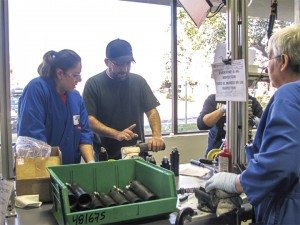
Oftentimes Fox tries new ideas in the aftermarket segment, and the OEMs add the shocks to their models after seeing them in action. Customers are also welcome to send their Fox shocks that come factory back to Fox for upgrades, instead of having to buy a new set.
In both aftermarket and the OEM side, the Powersports segment is performing well. Side-by-sides, not surprisingly, have been the biggest drivers of the growth. And though the bicycle division is Fox’s biggest, the company sees the most opportunity in motorized vehicles.
“We think between Off-Road and Powersports, which we called powered vehicles, we think that has the most potential for growth in the future,” Larson said.
Fox museum photos
Dan Robbins, corporate marketing manager of Fox, gave PSB managing editor Liz Keener a tour of the Fox museum at the company’s headquarters in Scotts Valley, Calif. The museum, which was built when Fox moved its HQ in 2012, chronicles the company from Bob Fox’s first prototype shocks to the current product, racing activities and more. To see some of the photos from Liz’s visit, check out this story in the digital edition of this issue. If you don’t currently receive the digital edition, visit http://bit.ly/1faJbHK to sign up.